River Tay Hydroelectric Project Success with Bradley & Co. and HydroNI
540m
2250mmØ Pipe
350 KG
Weight per pipe
130m
Radius with short pipes
Bradley & Co.’s Aquaspira Pipe Recommendation: Powering Grandtully Hydroelectric Project
Following the successful completion by Bradley & Co. of major project for Northern Ireland Water using Aquaspira pipes, the contracting partnership of Bradley & Co. and HydroNI recommended the use of Aquaspira Composite Steel Reinforced pipes to their client for a new Hydroelectric Power project alongside the River Tay at Grandtully, Pitlochry.
540m of 2250mmØ Headrace Pipe and 50m of 1350mmØ Tailrace Pipe were required to complete the low head, run of river project.
Challenge
- There was a high probability that the ground would be saturated during the construction phase, making it impossible to utilise a pipe system that would require in-situ welding of joints. Only a pipe system with manufactured sealed joints could be considered.
- For such a long run of large pipes, it was important to be able to progressively excavate, lay, and backfill the pipes efficiently.
- Access into the site was not only very constrained in relation to space, but there were also weight limits on the most direct route to the site entrance.
- The route of the Headrace pipe run necessitated a gradual curve with a critical design remit to ensure minimal head loss.
Solution
Aquaspira’s innovative and environmentally conscious solution included:
The spigot & socket, push-fit joints, with integral seals on Aquaspira pipes would provide an immediate sealed joint that can be completed in any weather, and even a slightly waterlogged trench, without any requirement for site welding.
The small OD of the pipes would keep excavation and backfill to a minimum, enabling the pipeline to be progressively installed and backfilled, eliminating risks from large, open excavations and piles of spoil.
Whilst each load would be optimised in terms of space (15.6m/load), the total weight of each full load of 6 pipes was only 2200Kg’s, enabling the most direct route to be taken.
The gradual radius to form the curved sections of the run was easily achieved through the use of a range of short pipe lengths that would enable minimal head loss and maximum versatility on site.
Outcome
Load optimisation, on standard articulated trailers, kept the number of loads to a minimum, using the shortest route possible. Once on site, the pipes were easily offloaded and distributed using small site machines.
As anticipated, the ground was partially waterlogged, however the integrally sealed joints on Aquaspira pipes enabled the joints to be made quickly and confidently.
The short pipes enabled the site team to set out and complete the radius sections with ease.
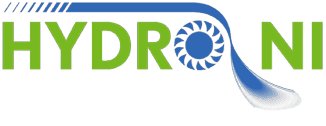
We found Aquaspira a great company to work with, and the pipes were easy and efficient to handle and install very. The overall solution, especially the short pipes to form the radius, worked very well indeed. Whenever we require larger diameter pipes we will certainly be recommending them to our clients
Gerard Murphy
Director | HydroNI